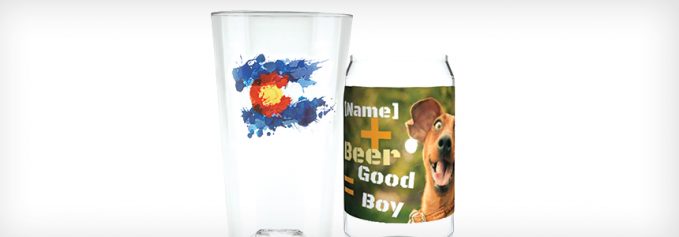
By Cassandra Balentine
The benefits of digital print have a noticeable impact on traditional print markets, including direct mail, transactional print, book printing, and signage. The technology also makes its mark on less obvious industries like labels and packaging and manufacturing.
The ability to print or decorate manufactured products on demand and in small runs is attractive as consumers seek more personalized experiences across the board. Recognizing this need, manufacturers consider the benefits of digital printing and how it can transform their business.
Based in Aurora, CO, GoRight Plastics, Printing, and Logistics, LLC (GoRight PPL) is a full-service contract manufacturing company offering in-house printing and labeling to existing customers as well as full third-party logistics. It customizes both in-house and outside manufactured products and handles delivery to the client or end customer. Digital printing is an important component of the operation; the technology provides the ability to produce short runs in a cost-efficient manner. This allows its customers to offer highly personalized items at low minimums.
“We are one of the few manufacturers in the country to offer in-house, short-run digital printing,” shares Kacey Stotesbery, director of printing, GoRight PPL.
The container manufacturer targets individuals, events, or organizations looking to customize its proprietary products, including The Perfect Pint line of drinkware; or mid- to large-sized companies seeking to produce one-off customization for clients. Additionally, an in-house development team works with startups and small businesses interested in exploring customization for their own products.
Above: GoRight PPL recently employed the K1 hybrid press to create giftable items for various states available in small quantities for a chain of giftware stores.
One-Stop Manufacturing
GoRight PPL is dedicated to helping its clients every step of the way, offering concept, design, and production services.
For manufacturing, it specializes in custom extrusion blow molding services for a variety of customers, supplying both commodity and consumer product manufacturing. Ready-made containers are available as well as custom products.
For custom manufactured containers, the team works with clients throughout the entire design process, including mold design, sample creation, and the full production run. The average production lead time for manufacturing is approximately 45 to 90 days and two to four weeks for customization. Custom product materials include PET, PVC, and HDPE plastics. All products are FDA approved.
The company believes it is important to decorate or print products at the point of manufacture. Therefore, it offers custom printing and labeling solutions provided at wholesale and direct to consumer. These include screen printing, pad printing, sticker/label adhesion, and digital direct-to-container printing. With its digital capabilities, small runs as low as one and low-volume consumer goods are possible. For larger volumes it provides bulk discounts.
Freight and drop shipping direct to end customer is available. The company delivers on demand solutions for warehousing, storage, kitting, and nationwide transport.
The Equipment
To customize its range of manufactured containers GoRight PPL relies on a range of decoration methods, including screen and pad printing as well as digital printing.
For its digital work, the manufacturer utilizes a K1 CNC-2500 from Koenig & Bauer Kammann (US) Inc., which offers a hybrid of digital and screen printing capabilities.
The machine prints on nearly any round, conical, or cylindrical item—such as a glass or ball. With it, the company can Pantone match any color ink. It offers both UV and solvent ink options for PVC, PET, glass, HDPE, metal, and polypropylene.
The K1 was originally deployed by the company to serve a customer looking to offer one-off customized glassware on its website. “They wanted the ability to add metallic accents to the prints so we decided on the hybrid machine,” shares Stotesbery.
When searching for a press for this purpose, GoRight PPL was specifically looking for a short-run machine that offered a decent run rate. Ease of operation and the ability to modify with conveyor systems to be operated by one person were two other features it required of the device. Despite looking into other solutions, Stotesbery says the K1 was the only machine to meet all of its qualifications.
Over time, she says a number of customers were intrigued and wanted to use the device to imprint metal, silicone, glass, and materials other than plastic. Its screen stations have allowed them to pretreat those materials to increase adhesion.
The company now utilizes the machine for approximately 16 customers, including its in-house drinkware lines.
In addition to the K1, GoRight PPL has a fully equipped, in-house machine shop. For manufacturing it primarily uses extrusion blow molding machines from Bekum America Corporation. The print shop includes the K1 as well as multi-color pad printers, four single-color screen printing units, and a number of automatic labeling and sticker application machines.
The Benefits of Digital
GoRight PPL has found the biggest challenge of digital to be entry into the market. “These machines are not cheap and take a lot of time to pay for themselves,” admits Stotesbery. “You also have to invest the capital with a production lead time of one to two years, and the training and startup time took us about four to six months all in.”
The company ordered its machine in early 2016 and were up and running by the end of 2017. “Overall the K1 has fulfilled a large need for our customer base, as increasingly consumer goods customers are wanting personalized product and they don’t want to order 288 of them,” says Stotesbery. “For any business that already does a lot of commodity printing, I would advise the K15 high-speed machine rather than the K1 given the different run rates. If your business focuses on small run applications, than the K1 is a great fit.”
Direct-to-object hybrid screen/digital capabilities allow GoRight PPL to complete print jobs for its customers as well as its own uses. “We have developed a fully integrated design studio where customers of The Perfect Pint website can design customized glasses, utilize and edit stock designs, or order seasonal designs at theperfectpint.com/collections/customization. The art is then uploaded directly to our server where our prepress team can access it and process the orders,” details Stotesbery.
Direct to Drinkware
Recently, GoRight PPL utilized the K1 hybrid press to create giftable items for various states available in small quantities for a chain of giftware stores.
The designs were state flag based and printed on plastic pint glasses. The in-house design team worked on the files, which were created using Adobe Illustrator and then digitally printed onto Tritan plastic drinkware. The dimensions measured 70×100 millimeters wide.
The number of possible prints created was 50 in run lengths of six glasses.
This type of project, with many versions of short-run work, is possible with the K1 digital printing press.
Custom Products, Customized
Manufacturers like GoRight PPL benefit from the latest printing technologies that enable cost-effective customization to attract modern consumers. With the capabilities afforded by the K1, the manufacturer stays ahead of the latest market demands.
Sep2019, Industrial Print Magazine